<-- zurück
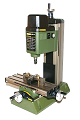
Die
Mini-Fräse MF70 von Proxxon. Der Preis liegt zwischen gut 200 und knapp 300 Euro. Es gibt sehr
viele Seiten im WWW, die über das Arbeiten mit der Fräse berichten. Hin und wieder wurde
von Problemen mit der Genauigkeit berichtet. Als das Gerät dann bei Voelkner für 204 €
zu haben war, die Kundenbewertungen fast alle positiv ausfielen und meine Frau sagte "Dann mach es
doch!" waren die Würfel gefallen.
Wenige Tage später war das Gerät da und ruck
zuck ausgepackt. Erste Enttäuschung: keine Fräser dabei, obwohl auf der Abbildung einwandfrei
zu sehen. Nun ja. Gleich in den nächsten Baumarkt und nach Fräsern geschaut. Es gab auch
welche. Auf einer Sorte stand "geeignet für ... Kunststoffe". Der war's. Hat etwa 8,- €
gekostet.
Vier Flächen á 2x5 cm² aus einer 3 mm dicken Kunststoffplatte (PVC?)
heraus gesägt und mit Sekundkleber aufeinander geleimt. Das gab einen schönen Block. Hieraus
wollte ich eine Halterung für einen Servo fräsen und zwar so, dass das Servo eine Lego-Achse
antreiben kann. (s. Projekt
Servo). Das erste Testfräsen
verlief zufriedenstellend. Als ich dann aber damit begann, das gewünschte Teil herzustellen,
traten die ersten Probleme auf. Nach jeweils etwa einem Zentimeter Fräsweg schmolz der Kunststoff,
setze den Fräser zu und der geschmolzene Klumpen Kunststoff zerrieb auch noch die nähere
Umgebung. Auch das Verringern der Eintauchtiefe half nur wenig. Zur Herstellung der Servo-Halterung
war dann doch noch Spachtel notwendig, um die Löcher zu kitten (u.a. deshalb auch die Lackierung
:-)).
Google sagt: einschneidige Fräser müssen es sein. Und am besten Polystyrol.
Beides habe ich jetzt. Die ersten Fräsbahnen sahen gut aus. Mal schauen, wie es beim nächsten
ganzen Teil wird.
Stand 17.2.2011:Auch die Fräse
hat so ihre Macken. Der Koordinatentisch hat Handräder zum drehen der Spindeln. Wenn man an
dem der X-Achse dreht, wackelt der ganze Koordinatentisch. Kann sein, dass das nicht viel ausmacht.
Ich befürchte jedoch das Gegenteil. Im Handbuch steht zwar, dass jede Ache mit einer nachjustierbaren
Schwalbenschwanzführung ausgestattet ist, mit der das Spiel der Führung nachgestellt werden
kann. Aber ich bin Anfänger und hatte gehofft, dass das Gerät werksseitig optimal eingestellt
sei. Außerdem weiß ich nicht genau, ob das "Spiel der Führung" das Spiel ist, dass
den Tisch wackeln lässt ... Ich fasse am besten zunächst gar nichts an, nachher geht gar
nichts mehr. Später sollte der geplante Motorantrieb nicht so ungleichmäßig an der
Welle ruckeln wie ich.
Die Z-Achse ist ganz schlecht. Sehr schwergängig und ein Spindelspiel
von rund einer Umdrehung des Handrads, also etwa 1 mm. Zwar sollte ein CNC-Programm ein Spindelspiel
berücksichtigen können, aber 1 mm? Das brachte mich auf die Idee, die Achsen nicht ausschließlich
nur über die Schrittzählung der Schrittmotoren zu steuern. Über preiswerte digitale
Messschieber kann man die Wege direkt messen.
Zur Fräse gibt es einen CNC-Umbausatz von
USOVO für gut 400,- EURO. Das war mir zu teuer und zu langweilig.
Also selbst ist der Mann.
Stand 29.5.2011:
Zum Umbau auf Motorbetrieb ist es unvermeidlich, einiges auseinander zu bauen. Das Spindelspiel wird über
Stoppmuttern eingestellt. Die kann man nachziehen.
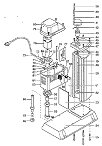
Ab einem gewissen Andruck werden wegen der Reibung die zum drehen notwendigen Kräfte recht groß.
Hier gilt es also ein sinnvolles Mittelmaß zu finden.
Das Wackeln der X-Achse ließ
sich durch Nachjustieren der Schwalbenschwanzführung reduzieren, aber nicht komplett beheben.
Erste Test mit dem Motor haben ergeben, dass hier die Kräfte gleichmäßiger auftreten
als beim Handbetrieb. Sichtbar wackelt nicht mehr. Auch hier: Kompromiss zwischen Präzision
und Beweglichkeit ist gefordert.
Die Schwergängigkeit der Z-Achse ließ sich ebenfalls
durch Justage der Führung beheben. Die war einfach nur zu fest eingestellt.
Fazit: Eigentlich
hatte ich erwartet, dass die Maschine ab Werk optimal eingestellt ist. Dies war offensichtlich nicht
der Fall. Insbesondere Anfänger, für die diese Maschinen gedacht sind, bereitet dies beträchtliche
Probleme.
<-- zurück